Have 3D Printed Bicycle Frames Finally Become a Viable Reality?
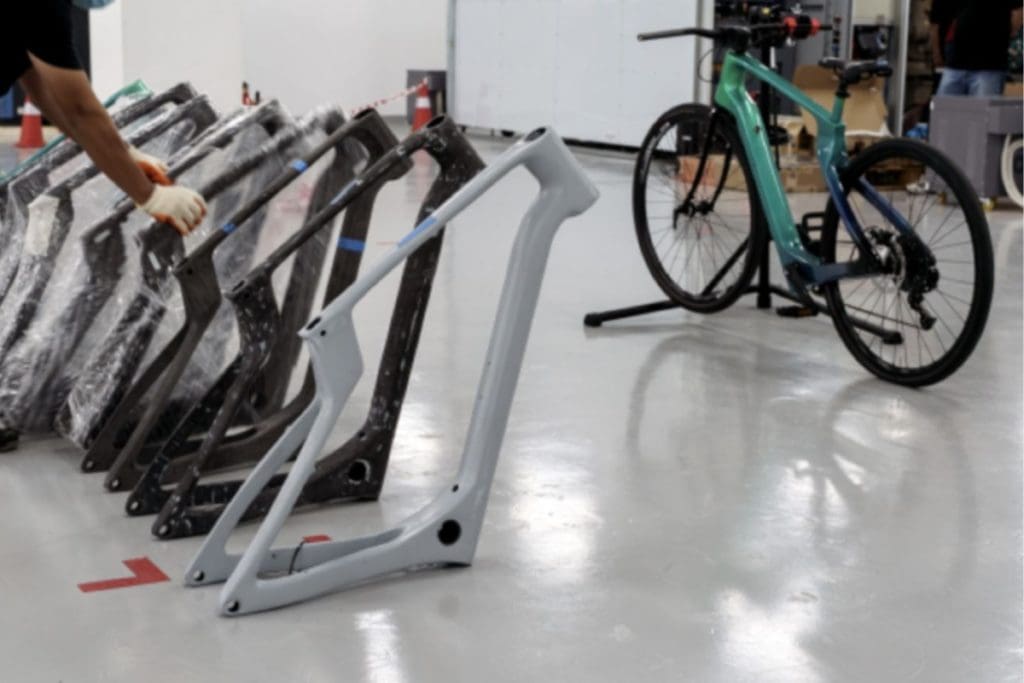
In global engineering and manufacturing, 3D printing has been big news for quite a while. In the case of bicycle frames, this means rather than joining pre-made tubes together with some form of welding or gluing, the entire frame is built from scratch in one process, by adding many fine layers in quick succession of whatever the frame material might be, such as titanium or carbon fibre.
It would have to be a decade already since we first started seeing reports of 3D printed bicycle frames. There has even been a failed Australian attempt, through Melbourne based Titomic with input from frame building and design veteran Peter Teschner.
But despite huge promises of efficiencies that would allow commercially viable custom production of bicycles even in high wage countries like Australia, we’ve yet to see anything beyond predictions and prototypes.
One of the challenges has been that the equipment and software engineering required to 3D print something as large and complex as a bicycle frame is very expensive.
But with the bike industry booming and more venture capital than ever flooding in, that hurdle has been overcome, at least by Silicon Valley (USA) based Arevo.
In early September Arevo announced not only, ‘the completion of the world’s largest 3D printing facility for carbon fibre composite additive manufacturing’, but also the first shipment of bicycles and e-bikes with frames made by their 3D printer.
During Eurobike 2019, Arevo presented a prototype 3D-printed carbon fibre composite bicycle frame. Since August 2020, they’ve been offering on-demand production of customised frames.
Now with the introduction of the next generation high speed additive manufacturing system for large continuous carbon fibre composite structures, Aqua 2, the production process has become four times faster than its predecessor.
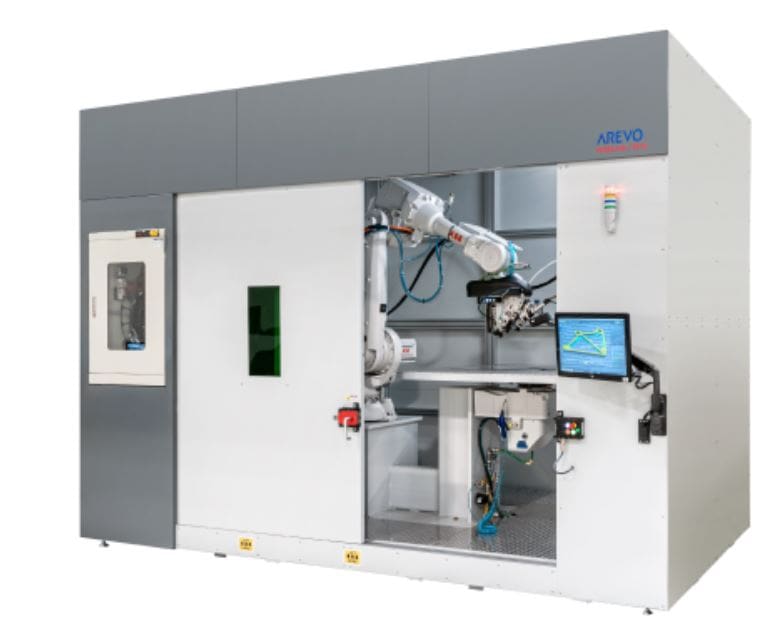
Arevo is operating a full range of production systems – including 70 Aqua 2 3D printers. According to one source the Arevo Aqua 2 3D printers cost US $500,000 (A$685,000) each.
In true Silicon Valley style, Areva has raised US$85 million (A$116 million) in funding so far, from some of the biggest names in venture capital.
According to Arevo, additive processes such as 3D printing enables, ‘fast, on-demand and comparatively cost-effective production’ compared to conventional methods. As a result, the company is using these systems to print not only bicycle frames and other sports equipment, but much more, such as automotive parts, aerospace components and even complex architectural structures.
Arevo CEO Sonny Vu said, “After introducing the Aqua2 3D printing system last year, which is four times faster than the Aqua 1, we have now focused on the production and operation of these systems. Currently, a total of 76 systems are in live production worldwide. They are all connected to the cloud and in use at our various sites. This puts Arevo in an excellent position to serve the growing global demand for both our own consumer brands and the needs of our B2B customers.”
Arevo’s own brands include Superstrata, a bicycle and e-bike brand, and Scotsman, an e-scooter brand. Coinciding with the completion of the new facility, Arevo has also shipped the first Superstrata bicycles and e-bikes with carbon fibre composite frames out of the 3D printer. In addition, the developers are just completing engineering for the Scotsman e-scooter.
Join the Conversation:
What do you think about the prospects of 3D printing for the bicycle industry?